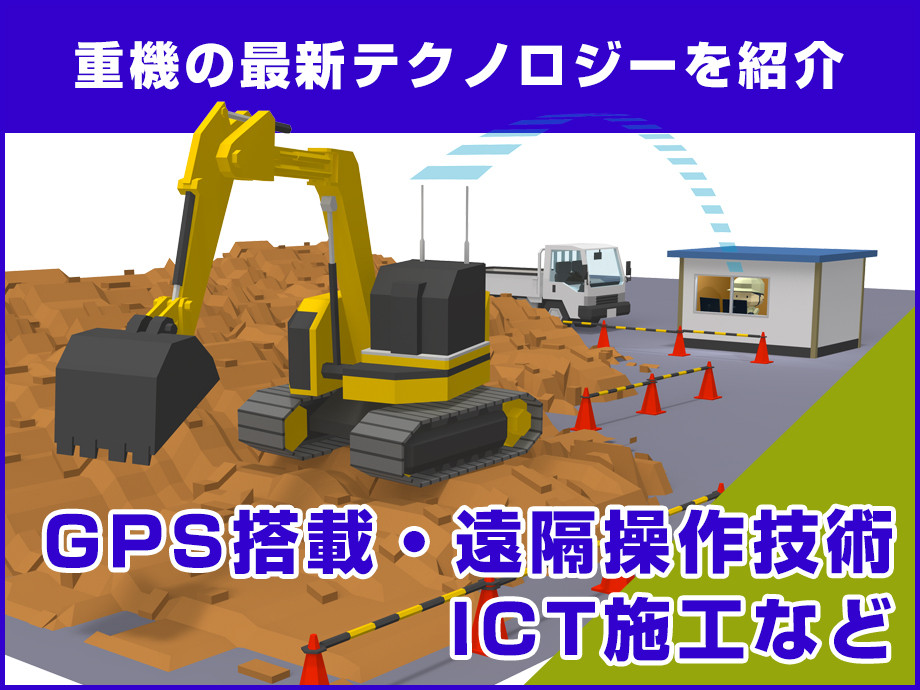
建機
2025/06/24
968
「工事現場の効率アップ!重機の最新テクノロジー」GPS搭載重機や遠隔操作技術、ICT施工など最新技術を解説
こうした課題を解決する鍵となるのが、最新の重機テクノロジーです。
GPSを搭載した重機による高精度な作業や、遠隔操作による安全性の向上、さらにICT施工による全体最適化などが注目を集めています。
本記事では、工事現場の生産性を飛躍的に高めるこれらの最新技術について、分かりやすく解説します。
無人施工で建設業の人手不足を解決!重機の最新テクノロジー
しかし近年は、少子高齢化に伴い労働現場での人手不足や、若者の建設業離れといった問題があり、現場の生産性向上といった課題解決が叫ばれています。
従来の方法ではこれらの課題は解決が難しいため、近年では”情報情報通信技術”を活用した、「ICT施工」や「無人施工」、「GPS」の技術を取り入れ生産性向上を図っています。
最新重機の導入で作業を効率化!未来の工事現場を解説
これに伴い、現場の生産性や安全性が飛躍的に向上しています。
AIによる制御や5Gを活用した技術を積極的に問い入れることにより、これから自動化に向けた動きはさらに加速していくことでしょう。
重機の進化|遠隔化・自動化重機の役割
この技術は人手不足に悩む、建設業界においては非常に注目されている技術です。
大規模プロジェクトやインフラ整備の現場を中心に、GPS、遠隔操作、ICT技術の導入が積極的に進められており、ダム建設や道路建設などの大規模工事において、その効果が確認されています。
これらの技術により、これまで長時間現場で行う必要があった作業を、オペレーターが現場に不在のまま複数箇所で同時に重機を稼働させることが可能になり、現場の生産性向上に大きく貢献しています。
GPS搭載重機の使用例
- ドローン空撮画像の3Dデータ化と重機のGPS連動
平成28年三重県伊勢市で行われた道路建設工事では、国土交通省が推奨する「i-Construction」を取り組みました。
ドローンによる現場の三次元測量を短時間で行い、結果を設計図面等の3Dモデル化することで切土や盛り土の量を自動で算出し、データをGPS搭載の重機へ送ることでほぼ自動で重機を稼働させ、現場の安全性と作業効率の向上で人手不足の解消にもつながりました。 - 機械位置情報システム
現場にある全ての重機にGNSSアンテナを取り付け、重機の位置を監視するシステムです。これにより位置情報をリアルタイムで画面に表示することができ、機械の運行状況なども瞬時に把握することが可能で、管理面や作業面の効率化に大きく寄与します。
建設機械メーカーのコベルコが開発した「KーDIVE®︎」と呼ばれる、重機の遠隔操作システム開発しました。操縦履歴や、遠隔重機データを活用することで、人と現場と重機をつなぎ、現場のDX化を目指しています。
GPS搭載重機の活用|重機のリモート化で得られる5つのメリット
- 「安全性の向上」遠隔操作・遠隔監視で危険作業を削減
重機の遠隔操作で得られるメリットとして「安全性の向上」があります。危険な場所や高所での作業を行う際は、現地で行わず離れた場所で行うためです。 - 「人手不足の解消」少人数オペレーションで人員と人件費を削減
重機の遠隔操作では、直接操作と、無線やネットワークを使った自動運転があります。そのため、今まで1台の重機にオペレーターが1人いましたが、遠隔操作が可能になると1人で複数台の操作も可能になり、人手不足の解消に大きな期待がもてます。 - 「作業の効率化」作業内容や進捗状況をデータ化して活用可能
無人施工を進める上で大事なのが、測量データや、作業データをデジタルデータ化し、後工程へフィードバックすることです。遠隔操作した作業履歴は全てデータ化され遠隔操作システムにて一元管理されます。そのデータは後工程や現在工事の遅れなどを瞬時に判断が可能になるため、効率的に工事をすすめられます。また、無人施工での作業データは、今後の改善活動へつながる重要なデータになります。 - 「時間の無駄を削減」複数重機を操作可能|現場への移動時間を省略
大規模な現場は山奥にある場合もあります。重機を遠隔操作ができれば、現場までの往復は不要になり、その分作業時間も確保できます。また現場責任者の現場巡視もリモートで可能になるため、移動の無駄を省けます。 - 「防犯対策の付与」GPSの位置情報で重機の盗難リスクを低減
GPSがついた重機は防犯対策にも役立ちます。あらかじめ稼働範囲と稼働時間を重機に設定しておくことで、設定外の時間や場所で稼働した場合にはすぐに、異常の通知が届くのですぐに対処可能です。そのため、現場においてあっても盗難を防ぐことが可能になります。
ICT施工の導入で現場管理を最適化
測量や重機操作、進捗管理までをデジタル化することで、作業の見える化と省力化が進み、現場全体の管理が最適化されます。
国土交通省が推進している「ICT施工」とは
情報通信技術を活用し、測量から設計、施工、管理に至るまでの全工程をデジタル化する手法がICT施工です。
各工程で得られるデジタルデータを活用することで、高精度な施工を効率的に実現し、作業の見える化や自動化により、施工精度の向上と省人化が可能になります。
「マシンコントロール式」と「マシンガイダンス式」の違い
MCは3Dデータに基づき、半自動的に施工を行う機能です。
一方、MGは、センサーやGPSなどを搭載した建設機械や車両が現場の状況をリアルタイムに計測・解析し、その情報をもとに人が遠隔操作を行う施工方式です。
これらの技術を活用することで、効率的な施工が可能になります。
国土交通省の「i-Construction」導入現場
河川工事、道路工事、土地改良工事など、多岐にわたる現場で導入が進んでいます。
ICT施工の全面的な活用を解説!
測量データを3次元で作成可能
これまでトータルステーションを利用した測量よりも圧倒的に早く、そして正確に測量が可能になります。
測量で得た計測データを3D化することで、遠隔操作や無人施工が可能になります。
デジタル技術を駆使して作業をリモート化
「自動制御型」と「支援型」の2つの操縦方法があります。
自動制御型は事前にプログラムされた通りに重機が自動で作業をします。
支援型は、作業者が離れた位置からしますがICT技術による支援機能があるためより正確な施工が実現できます。
センサーやカメラを利用して事故発生を抑制
重機自体にセンサーやカメラを設置することで、作業者や重機同士の接触事故を抑制できるため、結果的に作業員の安全確保が可能になります。
自動制御で施工品質が向上
そのため設備や配線の正確な配置と寸法精度が向上し、高品質な施工が可能になります。
作業の効率化で工期短縮、環境負荷低減に寄与
無人施工に関わる3つのデメリット
- ランニングコストが高い
システム全体や重機に取り付ける部品等のコストがかかるので、これまでの重機に比べると割高になります。 - 自社での人材育成が必須
スキルを持った技術者が不足しています。直接重機にのって操縦するわけではなく、遠隔地からのリモートなので従来の重機を操作していたオペレーターが遠隔操作になれるまでには時間がかかります。 - 対応できない現場もある
狭い現場では、無人化のメリットを最大化できないため、無人化ができないと言えるでしょう。
まとめ
建設業界の課題である人手不足対策や作業の見える化にもつながり、今後の現場管理に欠かせない存在となるでしょう。